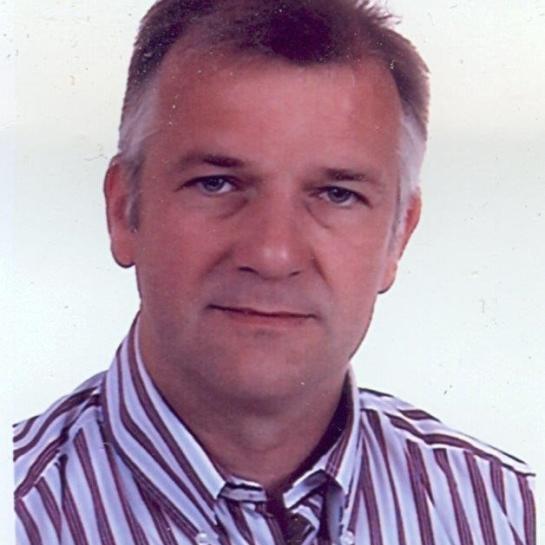
Acronym: Smartweld
Title: Smart welding of sustainable composites for medical applications.
Call: Eureka Cluster collaborative Project
ID: C0D88336-0796-4129-9731-9984796B3524
Period: 24 months: January 1st 2024-December 31st 2025
VUB Budget: €337.000,00
Contact: prof. dr. Danny Van Hemelrijck
https://memc.research.vub.be/nl/danny-van-hemelrijck
At ERIS we had a chance to talk to Danny and ask him 2 questions:
What is the context of SmartWeld and how is it linked to the medical sector?
The ‘Radiotherapy Treatment Devices’ sector is expected to record a significant worth of 9.6 billion € by 2028 due to the high growth of cancer patients and increased diagnostics.
The aim of SmartWeld is to develop a technology platform which integrates thermoplastic composite materials into radiational oncology and magnetic imaging medical applications. Currently, material solutions are dominated by thermoset composites. Thermosets, while extensively used, are less environmentally friendly materials and more difficult to recycle. Thus, medical solution providers are looking for sustainable, cost-efficient solutions to replace thermoset CFRP (Carbon Fiber Reinforced thermoset Polymer) matrix composites that can also be scaled up to meet the prognosed higher demand for these medical products.
Can you illustrate this with a practical example?
During radiation therapy or magnetic imaging, patients are positioned and immobilized on structures, commonly called “couches”. Accurate positioning and immobilization are both critical, as the delivery of the therapy, or the successful imaging, rely on the performance of the couch.
The requirement by clinicians is that the couches need to be as radio transparent as possible, to minimize the interaction between the treatment beam and the patient. To achieve high radio transparency, the couches and all accessories attached to it need to be low density, hence the reason for using composite materials. Today, interest in long fiber reinforced thermoplastic composites has grown a lot during the past few years due to an increased focus on sustainability and recyclability. Nonetheless, these types of materials have currently a very limited use in real applications. The reasons are the difficulties in processing due to the thermal cycling requirements and the higher temperatures required compared to thermoset resins, as well as due to the high material cost. So, SmartWeld is about to change this by introducing new materials that are more cost-competitive, easier to process and which are offering novel processing solutions. In this SmartWeld project the consortium will showcase -on an academic and industrial level- how these new composite materials have conquered the 4 major constraints of: cost-effectiveness, high-performance, lightweight solutions offer, and easy recycle.
What will be the impact?
SmartWeld will definitely have a multiple impact for the region of Brussels. Effective implementation of the project and subsequent reliable results will impact the medical sector since the new parts can be used in different hospitals and clinics. Environmentally, Brussels will indirectly benefit from the research on thermoplastic composites using different recycled material systems. The gain of benchmarking expertise at VUB on the use of recycled thermoplastics for different applications can open the way towards more sustainable and eco-friendly material structures. The experience that VUB will gain on the testing of thermoplastic composites will certainly offer more research opportunities. Being it either based on the new ‘know-how’ on thermoplastic welding technology either on novel research insights into the medical sector, SmartWeld will boost the VUB towards next cross-fertilization and interdisciplinary industry collaborations.